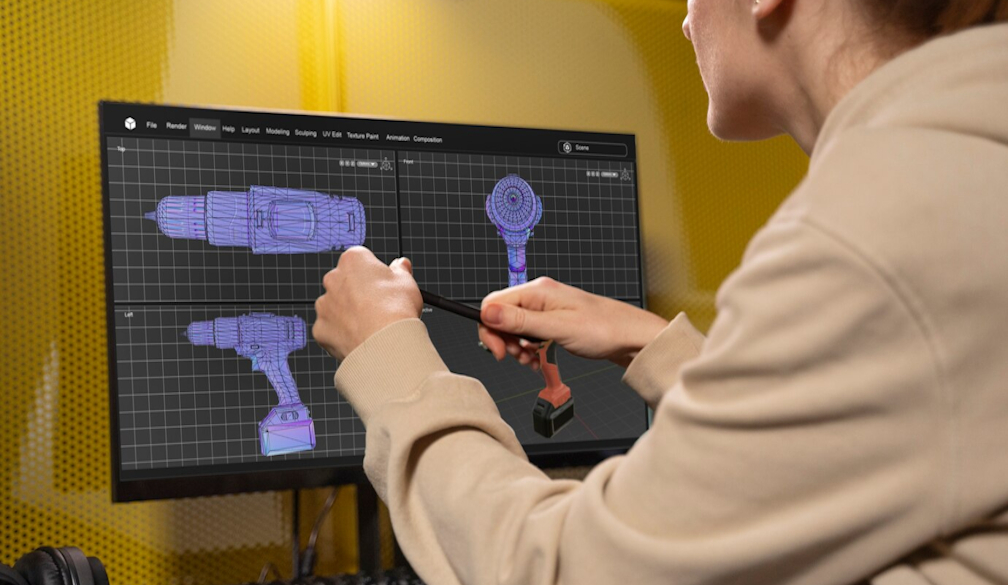
Engineers across industries—from aerospace to automotive manufacturing—rely on specialized tools that deliver exacting force measurements to secure components according to manufacturer specifications. The application of precise rotational force during assembly processes directly influences joint reliability, component longevity, and overall system performance. The torque wrench stands as the definitive instrument for this critical function, enabling technicians to apply specific amounts of turning force measured in foot-pounds (ft-lbs), inch-pounds (in-lbs), or Newton-meters (Nm). This specialized tool has evolved significantly since its 1918 invention by Conrad Bahr, incorporating advanced materials and digital technologies while remaining essential for quality-controlled assembly operations in professional and hobbyist environments alike.
Prevents Fastener Failure Through Precise Tension Control
Torque wrenches prevent catastrophic fastener failure by ensuring bolts and nuts receive exactly the force needed—no more, no less. When fasteners are overtightened, they experience excessive stress that can lead to thread stripping, bolt stretching, or complete failure. Research from the Mechanical Engineering Department at MIT indicates that approximately 23% of mechanical failures stem from improper fastener tension. Undertightened connections create equally problematic scenarios, allowing movement between components that accelerates wear and can lead to fastener loosening under vibration. Modern torque wrenches provide accuracy within ±3-4% of reading, allowing technicians to achieve the precise clamping force specified by engineers, typically 75-85% of the fastener's yield strength for optimal performance.
Ensures Critical Safety Standards in High-Stakes Applications
In aerospace, medical equipment, and automotive safety systems, precise torque application directly correlates to operational safety. Aircraft maintenance requires exacting adherence to torque specifications—the FAA has documented cases where improper torque application contributed to significant mechanical failures. Similarly, automotive brake systems depend on correctly torqued components, with manufacturer data showing that properly torqued caliper bolts can increase braking efficiency by 8-12% while reducing wear-induced noise. The consistency provided by calibrated torque wrenches ensures these safety-critical connections maintain their integrity throughout normal operation and extreme conditions alike.
Extends Component and Assembly Lifespan
Technical research from the Society of Automotive Engineers demonstrates how proper torque application extends component life by reducing stress concentration and preventing uneven load distribution. Engine head bolts torqued according to specifications show 40-60% longer service intervals before requiring retightening. In industrial equipment, correctly torqued flange connections experience significantly reduced gasket failure rates, with studies showing properly torqued connections lasting 3-5 times longer than those assembled without controlled torque. This directly translates to reduced maintenance frequency and lower lifetime operational costs for complex mechanical systems.
Maintains Warranty Compliance and Quality Assurance
Manufacturers increasingly specify exact torque values as part of warranty requirements. Documentation from major automotive manufacturers reveals that approximately 30% of warranty claims involve fastener-related issues, with many rejected due to evidence of improper torque application. Quality assurance protocols in manufacturing environments now regularly incorporate torque verification steps, with ISO 9001 compliance often requiring calibrated torque tool usage and documentation. Using calibrated torque wrenches provides verifiable proof that assembly occurred according to engineering specifications, protecting both manufacturers and consumers from premature component failures.
Enables Repeatable, Consistent Assembly Processes
Modern manufacturing demands consistency across thousands of identical assemblies. Instrumented studies comparing manually tightened fasteners against torque-controlled assembly show variation exceeding 45% in resulting clamping force when torque isn't controlled. Calibrated torque wrenches reduce this variation to under 10%, enabling standardized assembly processes across multiple technicians and facilities. This consistency proves particularly valuable in distributed manufacturing operations where components assembled in different locations must maintain identical performance characteristics.
Reduces Costly Downtime and Repair Expenses
Analysis from industrial maintenance departments indicates that fastener failures account for approximately 19-23% of unplanned equipment downtime. The average cost associated with such failures, including lost production, often exceeds the initial equipment investment several times over. Preventive maintenance programs incorporating proper torque specifications have demonstrated downtime reductions of 27-35% in manufacturing environments. The modest investment in quality torque tools yields substantial returns through enhanced operational reliability and reduced emergency repair scenarios.
Facilitates Precise Disassembly and Reassembly Cycles
Engineering components often require multiple service cycles throughout their operational life. Research indicates that fasteners properly installed using calibrated torque are 35% more likely to be removable without damage during subsequent maintenance. This preservability of threaded connections significantly reduces replacement part requirements and maintenance time. Furthermore, torque wrenches with angle measurement capabilities allow technicians to monitor fastener rotation during tightening, providing critical data about thread condition and potential failure modes before they manifest as operational problems.